|
 |
|
Fixed orifice steam traps |
These are devices containing a hole of predetermined
diameter to allow a calculated amount of condensate to flow
under specific pressure conditions. In practice, condensate
loads and steam pressures can vary considerably. For instance,
start-up and running loads can differ considerably along with
steam pressure which will change due to the actions of temperature
controls. These varying conditions can result in the fixed
orifice either holding back condensate in the process or passing
live steam, which can affect plant performance and compromise
safety.
Fixed orifices are often sized on running conditions, so
that they hold back enough condensate and do not pass steam.
If this is so, at start-up, they are undersized to a greater
degree and the steam space stands a good chance of waterlogging.
The alternative is to size them so as not to waterlog during
start-up. The hole is then effectively oversized for running
conditions, and the device will pass steam. The size of
hole is usually a compromise between the two conditions,
such that, at some points in between, the hole is correctly
sized.
|
Corrosion and service life of plant
Continual waterlogging significantly increases the risk of
corrosion in the steam space. It is not unusual to find that
after fitting fixed orifice traps, plant service life is reduced
below that which may be expected with proper steam traps.
A proper steam trap should be able to achieve just sufficient
capacity at all pressures and flowrates present in the application.
It can then pass hot condensate without leaking steam under
any condition. To achieve this, the size of the hole must
vary in the trap. It must be large enough to meet the worst
condition, and then have some means of reducing the effective
orifice flow area when the capacity becomes too great. This
exactly describes the operation of a steam trap.
|
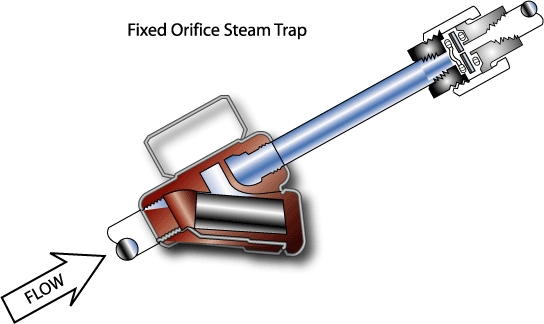 |
|
|
Advantages of a fixed orifice trap
Can be used successfully when pressures and loads are constant.
There are no moving parts
Disadvantages of a fixed orifice trap
If sized on running load, fixed orifice traps will waterlog
on start-up, reducing plant performance over this period,
increasing start-up times and the risk of corrosion. If
sized on start-up load, fixed orifice traps will waste steam
when the plant is running, effectively
increasing running costs.
Fixed orifice traps often block with dirt due to the small
size of orifice.
The cost of replacing a heat exchanger due to corrosion
will be far higher than the cost of replacing the fixed
orifice trap with a steam trap.
Note: Fixed orifice traps are not recommended for draining
condensate from any application susceptible to varying load
conditions. > |
Do They Save Energy Compared to Conventional
Steam Traps?
The answer to the energy savings question really is "it
depends." In order for a fixed orifice steam trap to
be effective, the condensate load must be relatively constant,
the orifice must be sized correctly, the steam should be clean,
pH must be controlled, and the strainer placed in front of
the orifice must be periodically blown down.
While vendors of fixed orifice steam traps claim both maintenance
and energy cost savings benefits, such benefits are difficult
to quantify. Fixed orifice traps continuously release condensate
and a small amount of steam, while steam losses from conventional
traps include cycling losses and losses due to the percentage
of traps that have failed in an open or partially open position.
Potential energy savings are related to the difference between
two unknown values: steam losses given existing system operation
with current maintenance practices, minus expected steam
losses after the orifice traps are installed and in use.
For instance, in "real world" operation, facilities
have populations of properly functioning and of "failed"
traps. A facility may have 90 fully functioning traps and
10 that have failed closed, open, or partially open. The
percentage of failed traps found is likely related to steam
pressure, trap type, and frequency of trap inspection and
repair.
A correct comparison of a base or conventional trap scenario
versus a fixed orifice scenario would compare the energy
losses from the 90 properly functioning and 10 failed traps
versus the steam losses due to using 100 orifice traps.
The orifice in fixed orifice traps is small compared to
the orifice in a conventional mechanical trap. Steam losses
from even a relatively small number of failed conventional
traps are substantial. It is this failed trap steam loss
value that must be compared with the losses due to the use
of orifice traps.
Key variables necessary to conduct an analysis include:
the percentage of failed traps, the orifice size for those
traps failing open or partially open, the mean time between
trap failures, and the steam trap inspection frequency associated
with the facility's maintenance program. After the losses
per failed trap are determined, the last two terms can be
used to determine the time (in hours per year) that a failed
trap would be expected to release live steam before the
next inspection/repair cycle.
Fixed orifice traps would likely save energy for systems
with a long inspection/maintenance interval and with large
numbers of failed conventional traps. Conversely, fixed
orifice traps could release more live steam than an existing
system where the percentage of failed traps is low. (Note:
manufacturers of fixed orifice traps contend that steam
losses through their traps are less than those associated
with brand new, properly functioning mechanical traps.)
|
|
|
|
|
|
|
|
|